Catalytic oxidation
When the amount of organics in the fluegas decrease, direct combustion becomes impossible without the addition of support fuel (typically natural gas) or alternatively you can use an oxidation type catalyst. A catalysts reduces the energy (temperature) required for combustion reaction to initiate. As a result a cayalytic oxidation can run at much lower themeratures and theryby much lover concentration of orhganics in the flue gas stream. The operating temperature in a catalytic unit may be as low as 200°C.
The use of a catakyst greatly reduces the OPEX for low VOC concentration systems, by elimination the need for support fuel and by allowing process equipment designed for much lower temperatures,
Catalytic VOC reactions
The reaction mechanism over the VOC oxidation catalyst is explained by the presence of active catalytic sites on the surface of the catalyst carrier. These sites have the ability to adsorb oxygen. In general, the catalytic oxidation reaction includes the following three stages:
- oxygen is bonded to a catalytic site,
- reactants, such as CO and hydrocarbons, diffuse to the surface and react with the bonded oxygen, and
- reaction products, such as CO2 and water vapor, desorb from the catalytic site and diffuse to the bulk of the exhaust gas.
The oxidation of hydrocarbons and CO in a flue gas can be described by the following chemical reactions:
[Hydrocarbons] + O2 = CO2 + H2O(1)
CnH2m + (n + m/2)O2 = nCO2 + mH2O(1a)
2CO + O2 = 2CO2(2)
Hydrocarbons are oxidized to form carbon dioxide and water vapor, as described by reaction (1) or—in a more stoichiometrically rigorous way—by reaction (1a). In fact, reactions (1) and (1a) represent two processes: the oxidation of gas phase HC, as well as the oxidation of OF compounds. Reaction (2) describes the oxidation of carbon monoxide to carbon dioxide. Since carbon dioxide and water vapor are considered harmless, the above reactions bring an obvious emission benefit.
Oxidation catalysts
Base metal catalysts
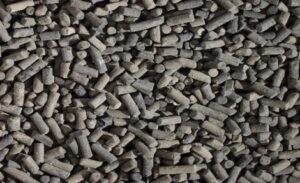
Copper and manganese on an alumina oxide extrudate. This range of catalysts, called NoVOC, is active to oxygenated hydrocarbons, e.g. ethyl acetate, acetone, ethanol etc. tolerant to silica and phosphorous. These properties, plus the significantly lower price than precious-metal catalysts, make NoVOC a the right choice for applications such as coating and printing.
.
Precious metal catalysts
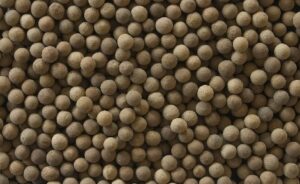
Precious metal (e.g. platinum) on an alumina oxide pellet. High activity to aliphatic and aromatic hydrocarbons, e.g. hexane, xylene, benzene etc. Long lifetime in certain key applications, which is important due to the high cost of platinum. As the standard version is easily poisoned by the use of silicon oils upstream, we also offer a silica-tolerant platinum catalyst, for chemical industry applications.
Honeycomb metal substrate catalysts
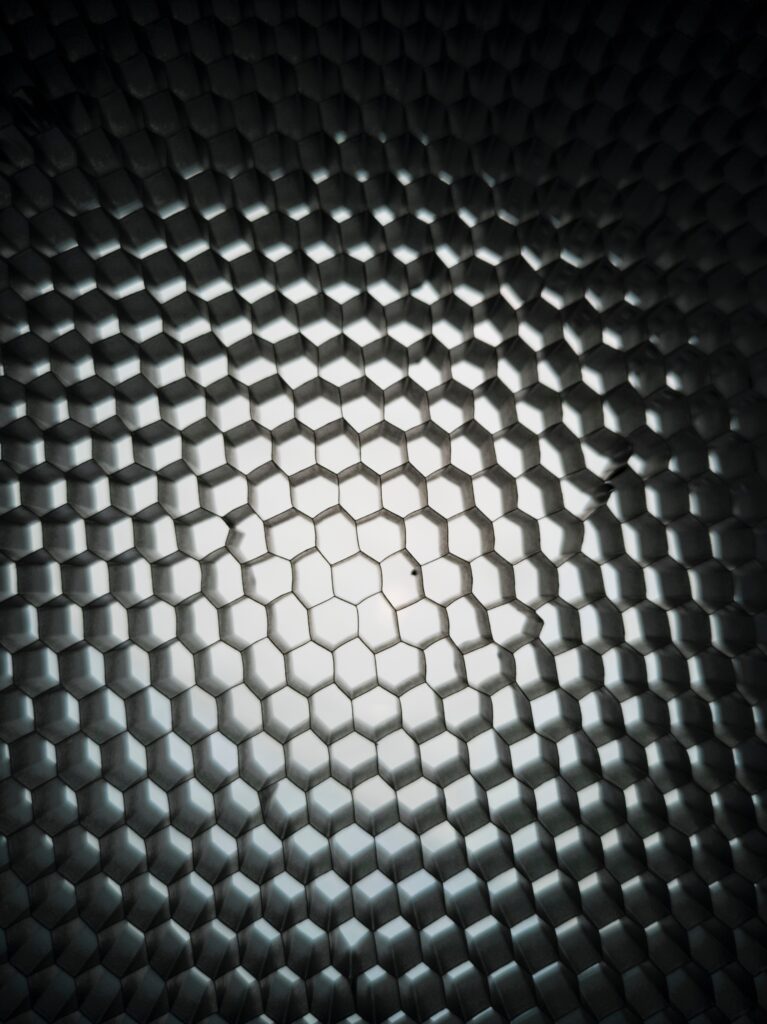
Precious metal on a metal substrate. These catalysts are used when the design criteria from the system supplier requires less catalyst volume compared to pelletized catalysts, or where linear velocity through the catalyst can be kept higher, e.g. in smaller reactors. The catalyst is supplied pre-mounted with mantel and flanges.